バレル研磨
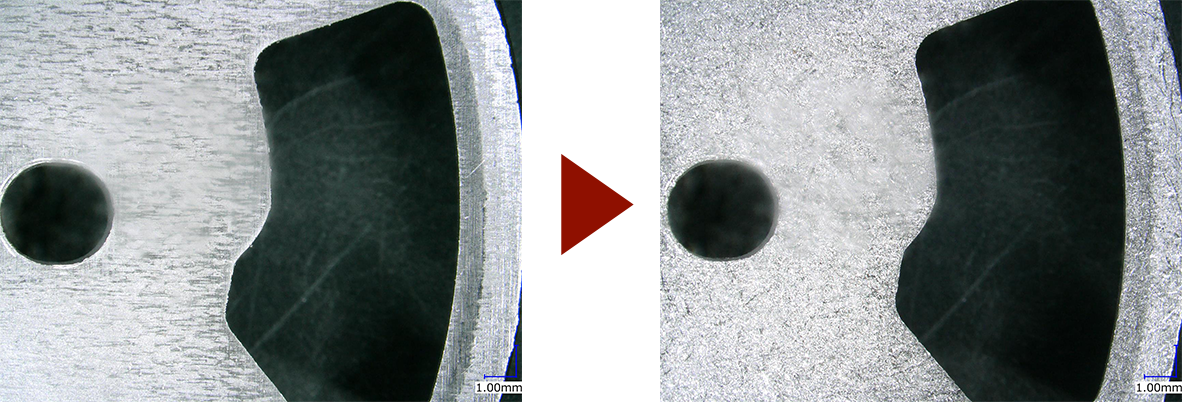
生産準備段階では想定していなかったバリが製品の一部に発生。製品全体の寸法は維持しつつ、部分的なバリの除去ができなければ、不具合品として廃棄せざるを得ない状態でした。普通にバレル研磨加工を行なうとバリは取れますが、他の部位の寸法が変わってしまい、これもまた不具合品として廃棄・・・。弊社では図面の寸法を順守のうえ、研磨加工を行なうことができ、お客様のご要望にお応えすることができました。
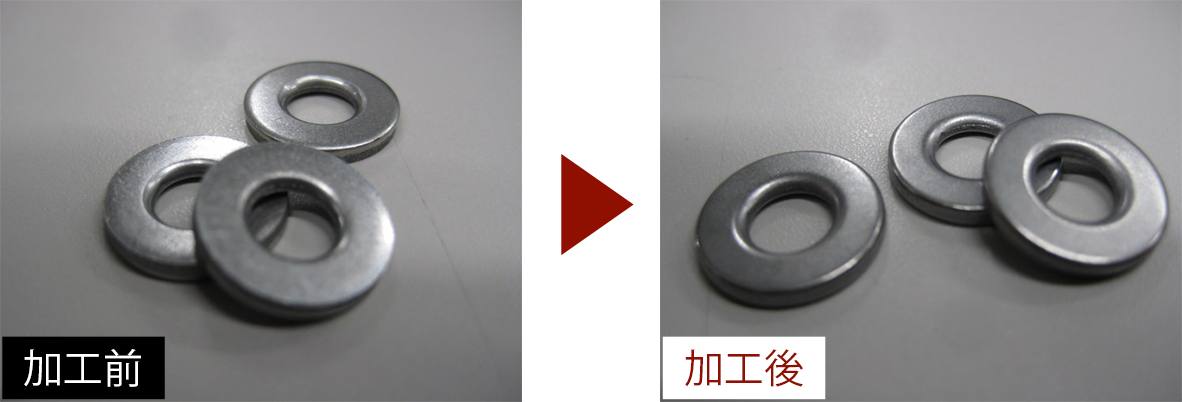
ワッシャーが組付けられた際、外周の角部が一定以上丸みを持っていないと締結時に相手物を傷つけてしまうとのこと。角部は製品によって状態がそれぞれ異なりますので、加工条件を慎重に設定していくことが必要です。テストを重ね、データを蓄積した結果、要求どおりの加工条件と加工手順を安定確立しました。
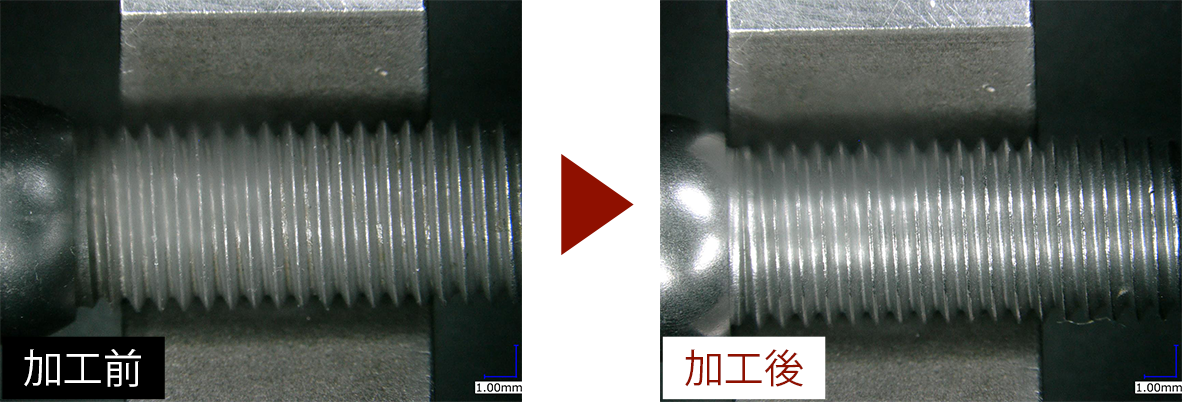
アジャスティングスクリュは内燃機関に使用する製品です。組付け後のカーボンスラッジによる不具合発生を未然に防ぐために、表面に付着したスケール除去を行いました。そうすることで、不具合の無い安心の製品となりました。
製品に付着したスケールを除去し、軽微なコンタミやシャープエッジを除去することで、パーツフィーダーで流れていく際のつまりを防ぎました。それにより通りをスムーズにしチョコ停の発生を抑えることができました。
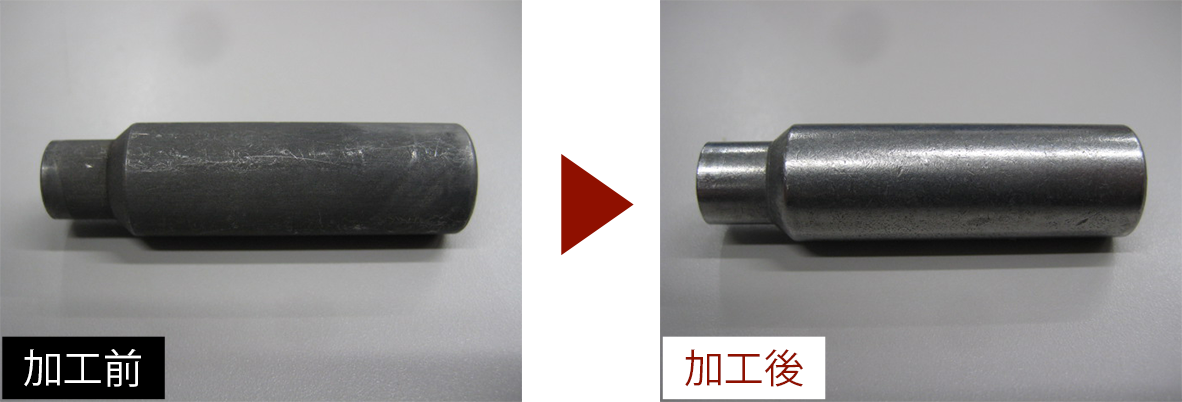
ボンデ被膜を除去してほしいとのご要望がここ数年特に増えています。冷間鍛造時に付着したボンデ被膜をそのままに真空炉で焼入れてしまうと、焼入れ時の熱によりボンデ被膜の成分が炉内に拡がり、炉内は真っ黄色になり炉内環境を汚染してしまいます。そのため、焼入れ時に強く求められることは、焼入れ前にボンデ被膜を除去しておくこと。当社の提案で、問題の原因であるボンデ被膜を除去でき、焼入れ工程での問題を解消しました。
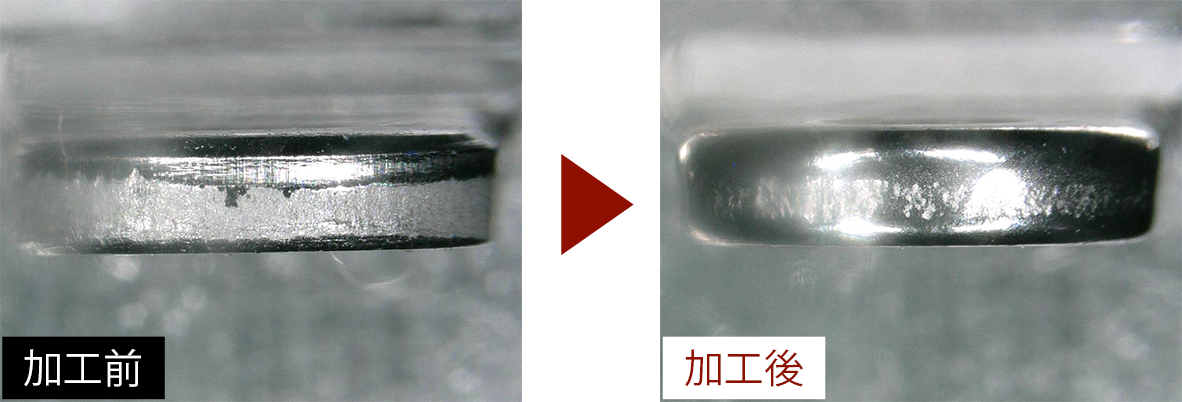
デジタルカメラ ストラップ用ブラケットを組付ける際に側面の荒い部分が、作業者の指先を傷つけたり、製品となった際はカメラストラップや衣類を傷付けてしまう可能性があります。また、除去されていない場合、見た目にも美しくはありません。バレル研磨加工+αの複合的な加工により、線断面除去と光沢仕上げ、2つの要望を高いレベルで実現した事例です。
素材や製品の状態を確認し、加工機や加工時間、研磨石等の細かな条件に対し最適な組み合わせを過去の加工事例より探し出すことで、顧客の求める要望に合った製品実現をお手伝いすることができました。
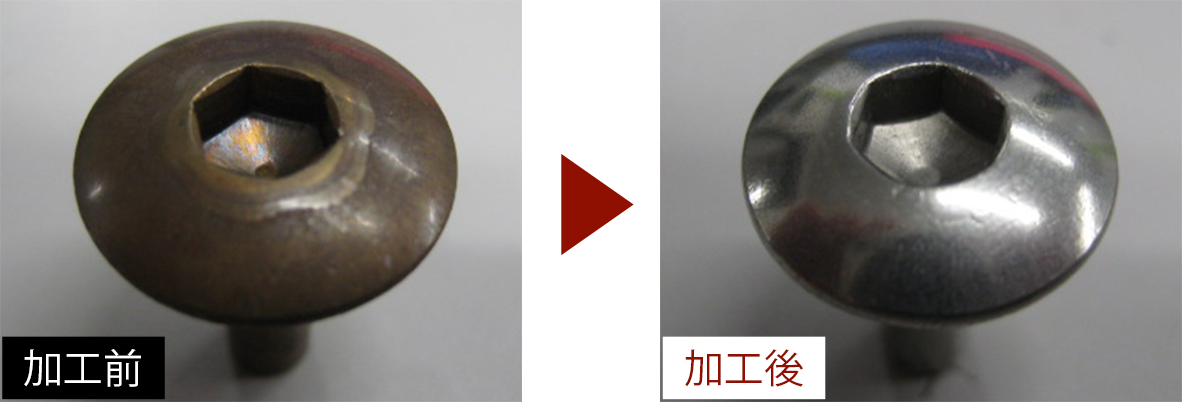
通常のスケール除去に加え、外装品であるステンレス製ボルトの仕上がりに光沢感を求められた製品です。弊社のノウハウでお客様のご要望にお応えすることができました。お客様立合いのもと、繰り返しの試作で加工の条件を何度も設定し製品実現に至った事例です。
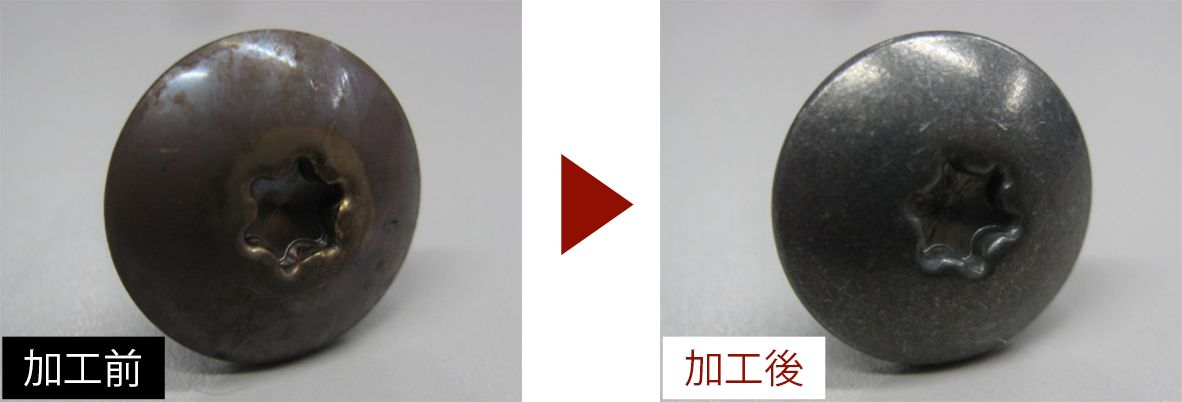
内装品であるボルトに、従来の塗装やメッキといった表面処理ではない方法で、電圧の微妙な差により変色させることができ、求める色合いを実現しました。塗装やメッキ処理のように表面の色が均一、同一になりにくい場合には非常に有効です。弊社で行った変色処理は、大きな満足を得ることができ、顧客から技術特別賞をとして表彰されました。
ワッシャーの溝の形状を保持しながら、ワッシャーの組付け時に悪影響である付着した加工油を除去して欲しいとのご要望。しかし本来見込んでいなかった工程のためコストをかけずに解決したいというご要望でした。バレル研磨機での処理(バッチ処理)により、まとまった数量を一括で処理出来たことによりコストも下げることができました。
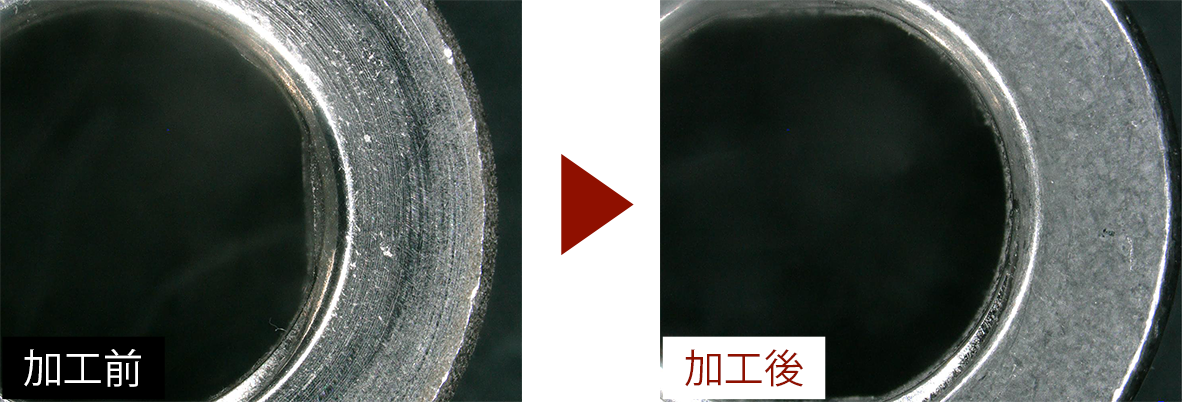
面粗度を向上させるだけであれば、それほど難しいことでありませんが、それ以外の製品の形状や寸法等、図面の規格にも合わせることが必要です。当社の前工程とも調整を行った処理によりお客様のご要望にお応えすることができました。
バフ研磨
自社でバフ研磨加工機を製作。手作業で行っていた作業を自動機で処理可能にしたことで、品質が安定し、かつ加工能力を格段に上げることができました。
ボルト頭部の切削加工を前工程と協議し、弊社受入れ時の面粗度の上限を設定することで、弊社での研磨工程が安定しました。結果的に次工程のダブルニッケルクロム処理も安定し、大幅な不具合削減につながり、かつ外観も美しい仕上がりとなりました。この顧客を交えた工程間の連携がその美しい状態を保てるカギとなった事例です。
エアブラスト加工
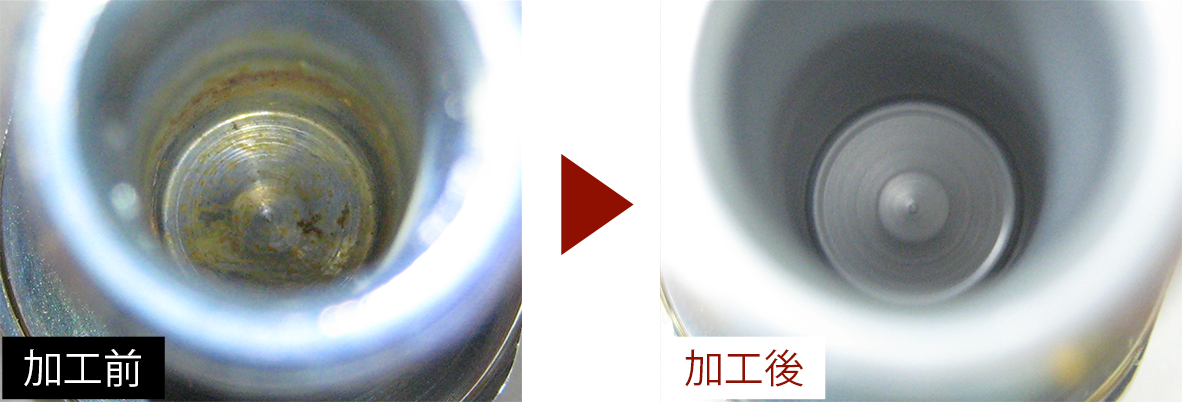
製品の形状上やむを得ないサビがメッキ後、深穴内部に発生。サビの発生した深穴が、内径の寸法1に対して深さがその約3倍の寸法。深穴の奥に発生したサビは除去するのが非常に除去しにくいのが一般的です。当社では、特殊な方法により深穴内部のサビを除去し顧客の要望にお応えすることができました。
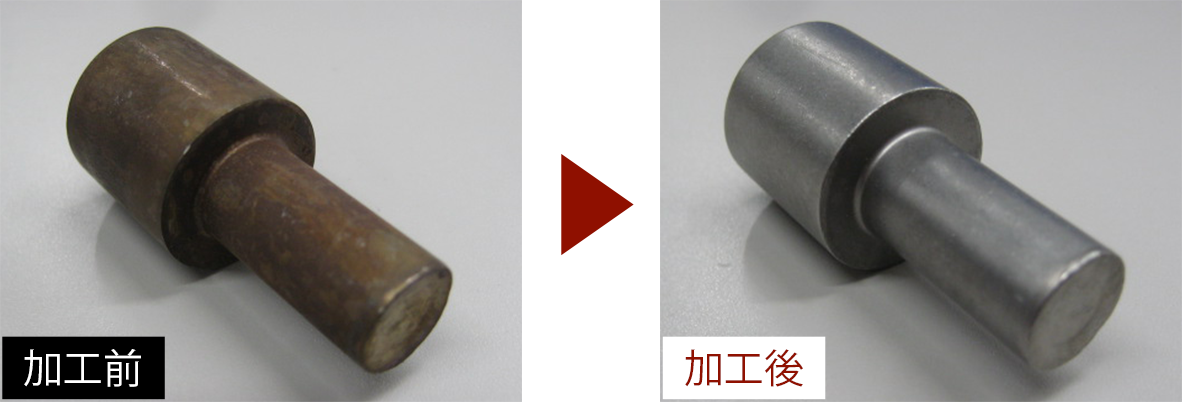
インペラー式のスチールショットと違い打痕等の製品への影響が少ない利点あります。製品の形状を保持し、寸法を守りながら顧客の要望に応えることができました。
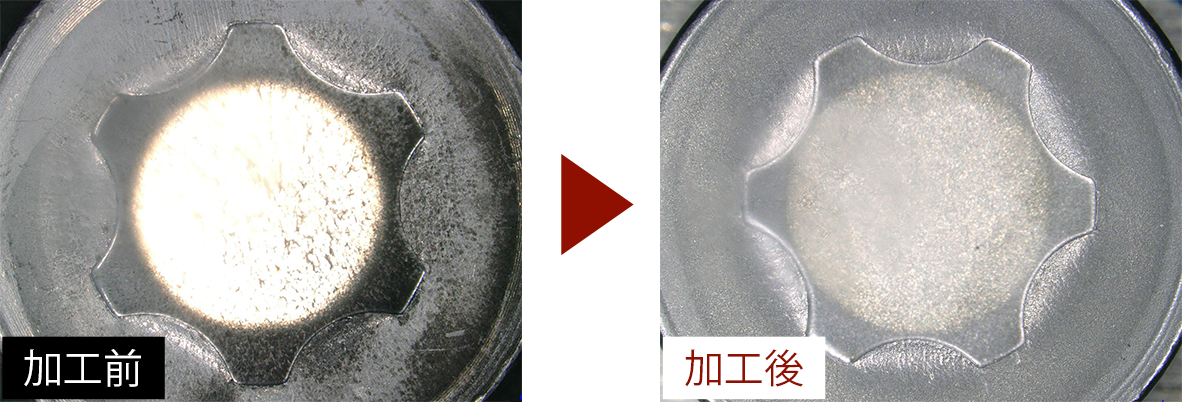
不純物(スケール等)により、部分的にメッキの未着が発生。全数検査による選別が恒久的に必要な状況でした。処理ロットごとに不良数もバラつき、酷いときにはほぼ全数が不良品になってしまうこともあり、対応に至りました。焼入れ後の不純物をメッキ処理前に除去することで安定した生産を顧客に提供することができました。
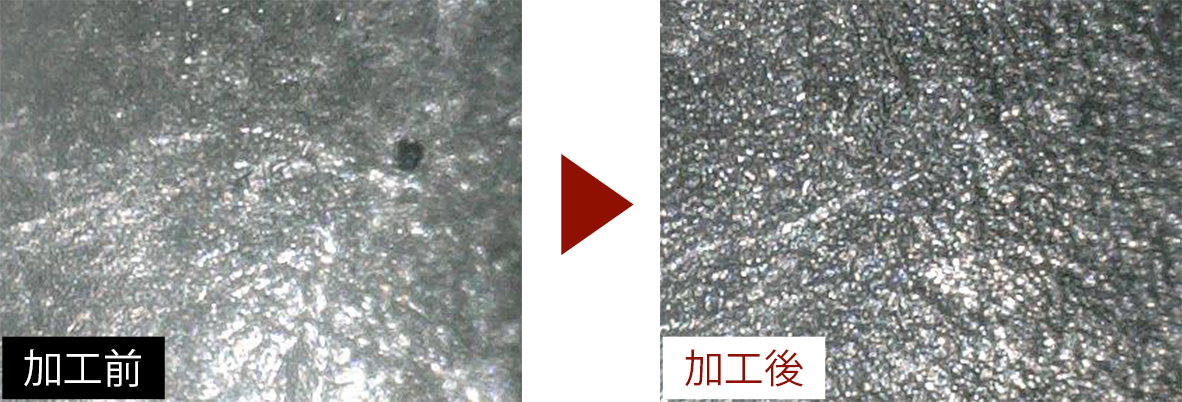
変色加工を施した外装品としてのボルトの色を落とすことなく、製品の表面に細かな凹凸をつくりました。ざらっと、よりマットな質感に仕上げることができました。梨地仕上げと言われています。
ブラシ研磨加工
ネジ転造が施してある製品のネジ山の取り扱いは非常に繊細さを求められます。
本製品もスクリュの軸先を切り欠き加工する際に発生するバリを除去したいが、ほかの部分は触らないという条件。軸先のみの加工を行い、形状がやや複雑な軸先の細部のバリを除去しました。
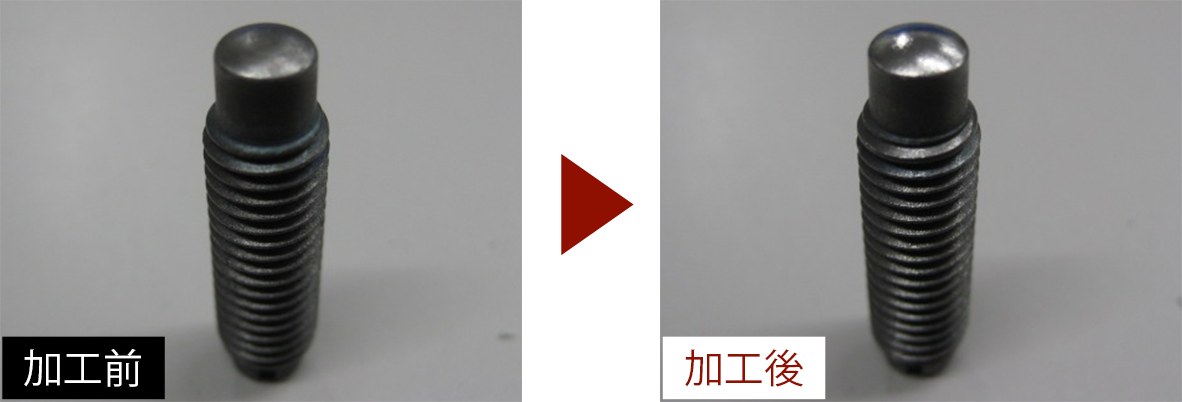
スクリュ頭部をブラシ研磨で処理することで、顧客が求める面粗度を実現しました。バレル研磨機での脱脂およびスケール除去も当社工程内でおこないました。
機械製作
自社で加工目的に対し自社開発にて機器を製作
当初の工程設計段階では、お客様所有の平面研磨機で加工する予定でした。しかし、お客様所有の平面研磨機は品質面では問題ないものの、非常に大がかりで社内での作業にも関わらず非常にコストがかかるとのことでした。お客様と打ち合わせを重ね、要求品質をしっかり満たすだけでなくコストに合う専用の平面研磨機を作製することで解決いたしました。
複合加工
生産準備段階では想定していなかった内径の口元に糸バリ発生。お客様は、この不具合に対し全数選別による糸バリの有無の確認と手作業でバリを除去されていました。バレル研磨加工で糸バリを除去することも試されたのですが、発生した糸バリが製品の形状に沿って張り付き、除去することが一層困難な状況になってしまったとのことです。当社は、バレル研磨加工だけではなく複合的な加工をご提案し、ご要望の内径の口元に発生した糸バリの除去にお応えすることができました。
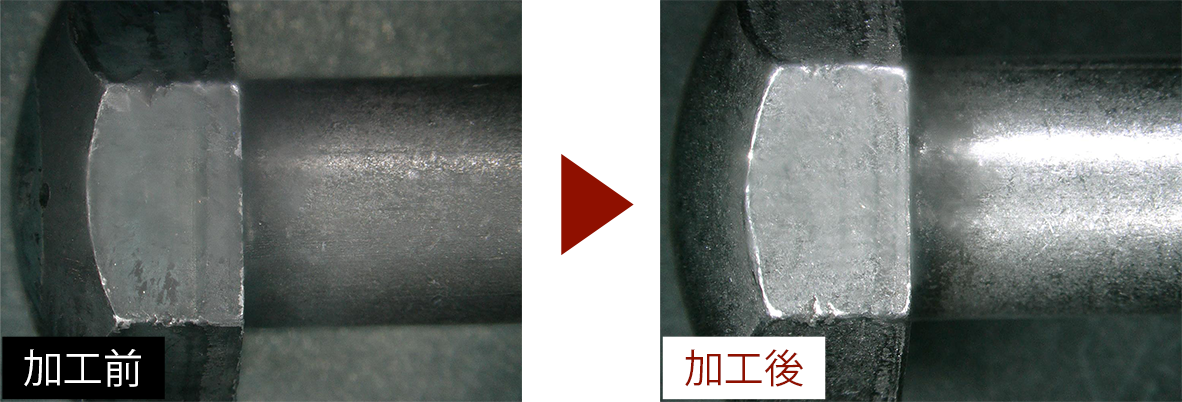
通常の熱処理後に行うインペラー式のスチールショットというスケール除去方法では、製品の形状や寸法に対して少なからず影響があります。当社のノウハウで行う処理により、形状や寸法に大きな変化を与えず、スケールを除去することができました。また今までの工程では、トリミング→バレル研磨→熱処理→スチールショットという流れが一般的でいたが、熱処理後のバレル研磨加工により、バリの除去とスケールの除去を一度の処理で賄うことができるようになりました。